DuraTEC
DuraTEC™ – Tempered Enamel Coating is specifically designed to eliminate the chronic problem of fouling and corrosion in airheaters as well as plugging commonly caused by Ammonia Bisulfate (ABS) on units equipped with SCRs. The objective of this revolutionary technology is to provide a longer life span of the heating element as well as improve or maintain the designed thermal performance of the surface configuration.
DuraTEC™ is a state-of-the-art technology advancement that incorporates metal oxide nano-particles a ceramic matrix, and special additives to produce a vitreous enamel coating that that minimizes cracking and deterioration in vertical or horizontal airheaters. The corrosion resistant properties consist of proprietary frit formulation (fused material that is the basis for enamels) and the use of special techniques and processes that are applied in multiple layers. DuraTEC™ utilizes various application techniques (wet enameling, dry electrostatic enameling and a combination of both) in conjunction with nano-technology to produce a strong amorphous bond with the steel. The enamel and steel “melt” together without delineation between the two layers. The advantage of this amorphous bond is that if the top layer of enameling is lost the underlying steel is still protected and resistant to corrosion.
Features and Benefits
DuraTEC™ is highly elastic, flexible and impact resistant. It incorporates properties that eliminate cracking problems associated with current enameled element and make it well suited for use in industrial applications such as airheaters.
DuraTEC™ incorporates a patent pending technology that gives it self-healing properties that minimizes cracks from propagating throughout the coating thereby extending useful life.
The DuraTEC™ surface is smooth, lubric and incorporates a “non-stick” nano-technology to reduce the surface wetability, creating a “Lotus Effect” similar to the properties of a lotus petal sitting on a pond. The surface cannot be wetted by water or acid, which provides additional resistance to buildup of ash, ABS and other deposits.
DuraTEC™ utilizes various application techniques (wet enameling, dry electrostatic enameling and a combination of both) in conjunction with nano-technology to produce a strong amorphous bond with the steel. The enamel and steel “melt” together without delineation between the two layers. The advantage of this amorphous bond is that if the top layer of enameling is lost the underlying steel is still protected and resistant to corrosion.
DuraTEC™ can also be supplied with SCR catalyst embedded on the surface of the coating to allow the hot layer of the airheater to utilize ammonia slip and act as an additional catalyst layer to enhance the reduction of NOx emissions.
DuraTEC™ has enhanced corrosion resistant properties that help address the harsh conditions that can be encountered in an airheater. DuraTEC™’s enhanced corrosion resistance is due to an improved manufacturing process for forming and cutting the element sheets. The process includes two separately formulated layers of vitreous enamel, a unique application method to assure uniform edge and ridge coverage, as well as proprietary steel that produces an additional corrosion resistant layer underneath the steel/enamel amorphous bond. The combination of technologies and improved manufacturing processes gives DuraTEC™ un-surpassed corrosion resistance well above that of standard enameling.
Technology
DuraTEC™ uses nano-technology to insure optimum adherence and bonding of the proprietary ceramic-vitreous frit to the pure and specifically prepared surface of the base metal. The application of this technology is achieved in six carefully monitored processes:
• Proprietary steel selection
• Raw material cleansing
• Six stage surface preparation
• Wet flow nano-modified frit integration and application
• Electrostatic ceramic-vitreous matrix implementation
• Temperature controlled heat treatment & cool down
The result of these processes enables the heating elements to have flexibility, corrosion resistance and a slick finish that can withstand severe environments.
This advanced nano-technology used in both the steel and the coatings achieve strong adherence to the base metal and between the multi-layered enamel surfaces.
The propriety nano-particle matrix additives achieve self-healing properties that stop and minimize crack propagation in the enamel.
Nano-modified enamel formulation produces elastic properties in the enamel that result in significant mechanical resistance of the enamel in both bending and impact loads.
The proprietary surface preparation technique of the base metal allows the materials to bond and create a unique corrosion resistant surface layer underneath the base coat enamel coating. There are three corrosion resistant layers under the exposed enamel:
• The base enamel coat
• The amorphous bond layer between the base coat and the steel
• The modified grain structure of the steel under the amorphous layer
The surface preparation enables the base metal to build a proprietary surface texture that works in a synergistic manner with the nano-particles to produce an amorphous bonding layer (the enamel morphs and becomes part of the base metal material similar to the manner in which a weld is formed in steel.)
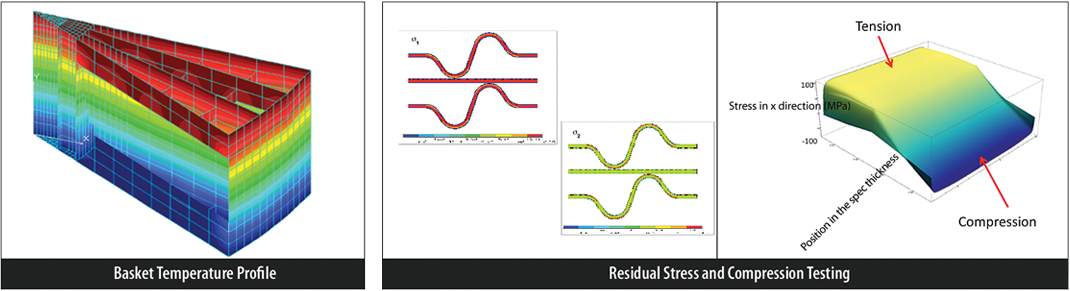
When they sent their service engineer out, he helped us, and he had their best knowledge that helped us out in ways we never expected. He had 25 years in power generation.

BGE
BGEWe purchased contact seals from Paragon. They are the only company that had this type of seal. That is why we went to them. The standard seals were wearing out prematurely.

APS
APSThe planners tend to feel comfortable calling a Paragon person and discussing a plan and talking through recommendations. There is a valued relationship there.

APS
APSI value the strong relationship with Paragon that I have. They have been very customer oriented.

APS
APSVery happy with the in-field service. There is loyalty to Paragon, based on the in-field service.

Black Hills Energy
Black Hills EnergyThey have a very good crew that did the installation. They came in early. They knew what they were doing, and I didn’t have to stay out their constantly, and they kept me informed.
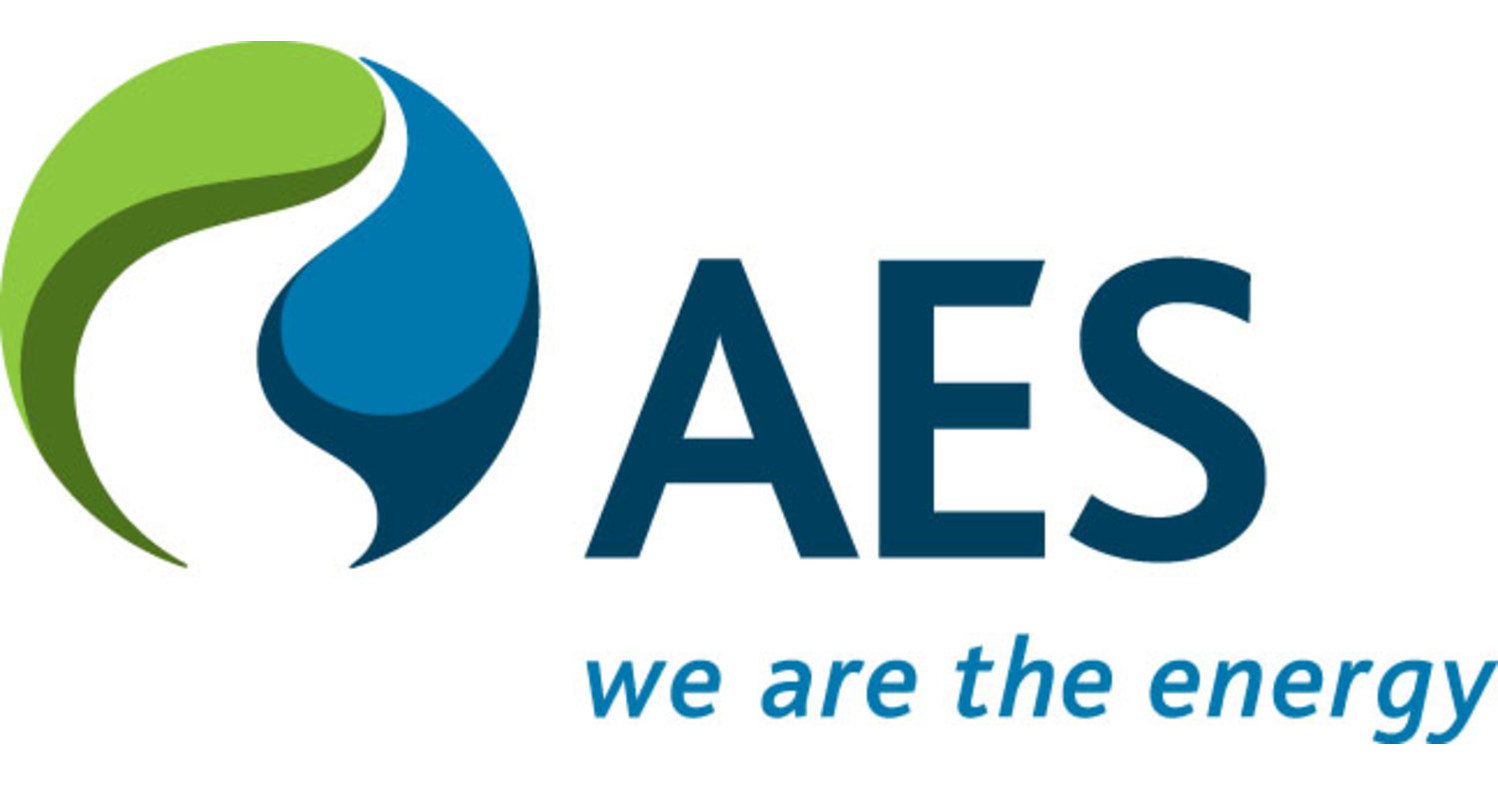
AES
AESYou get more of a personal care, because they are a smaller company. I work for a number of plants. I would and have recommended Paragon. I have that confidence.
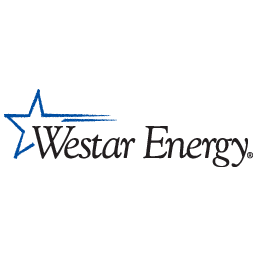
Westar Energy
Westar EnergyCustomer service is the main reason for our loyalty. You always find things that are not planned for, so we need it flexibility and great service a lot during outages.
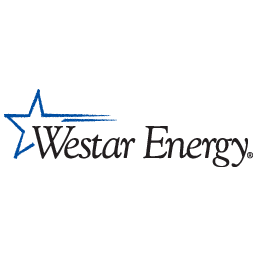
Westar Energy
Westar EnergyThe customer service is what makes them unique. That is it by far. Plus, you could also say having more innovative designs. Giving the customer more options than just OEM replacements.

Mirant
MirantParagon has better customer service. They are easier to get a hold of and really seem motivated to get you answers.

Mirant
Mirant“The biggest benefits from Paragon are a better after market product, and they help me prove to my management on what we are getting (pay for performance)

Mirant
MirantWhen they say something is going to happen, they deliver on it. Trust is really important. Less time for me worrying overseeing

Mirant
MirantWhen they say something is going to happen, they deliver on it. Trust is really important. Less time for me worrying overseeing

Mirant
MirantThe relationship is a little more collegial with Paragon than others. They are out to solve my problems with me. When they say something is going to happen, they deliver on it.

Mirant
MirantOnce you use Paragon’s seals, it is very clear that it is better. It just maintains the seals longer.

Midwest Generation
Midwest GenerationAll the technical guys, field reps are great. When I call they are available

Midwest Generation
Midwest GenerationI would call them a partner. They have the engineering background that the younger engineers here don’t have. I am buying a technical product. Their service engineering is just as important as their product.

Midwest Generation
Midwest GenerationWhat they said, they delivered. Meaning, they will stand by you if something goes wrong

Southern Power Company
Southern Power CompanyParagon earned our loyalty through the people first. When there was a problem they made it right. They have really good ideas and good service. And they stand behind their products.

Deseret Power
The Paragon technical supervisor provided was a real help to us on our project. We were pleased with his assistance and knowledge of our Ljungström pre-heaters. I’m keeping his and your contact information for any future shutdowns…
